Materials handling equipment is pivotal in the manufacturing sectors, from general distribution to the process or assembly of the manufactured part. Typically, most raw materials delivered into a factory are palletised and off loaded from delivery vehicles by FLT.
Once the pallets have been signed in then often the stock is required to be decanted and distributed either to storage or straight for processing. Pallet conveyor is a heavy-duty roller conveyor that can be powered or gravity and is used to move pallets around before being decanted or part of the decant operation. Once parts are decanted, smaller items can be placed onto different conveyor lines such as belt conveyor or power roller conveyors that you may typically have seen in warehouses. Sensors and control systems can be incorporated with barcoding, so the system knows where to send each individual item.
When items are in position ready for processing this might include cutting, welding, machining etc. Hot works would require a heavier duty steel slat conveyor or typical roller conveyor which can be built into CNC lathes and other machinery.
When a product has been fully fabricated or built then often cleaning, prepping and finishing may follow. Metal parts may require degreasing in a pre-treatment or acid pickle for high tech components for the aerospace industries. Once cleaned a protective coating of either wet & powder paint or a typical anticorrosive galvanizing or BZP. Overhead chain conveyors are often ideal in these instances as finishing plants have numerous different stations and processes that require access to all sides and angles of the product. Where several finished items are required to be put together then assembly lines will often take advantage of belt or inverted chain conveyors to assist with process.
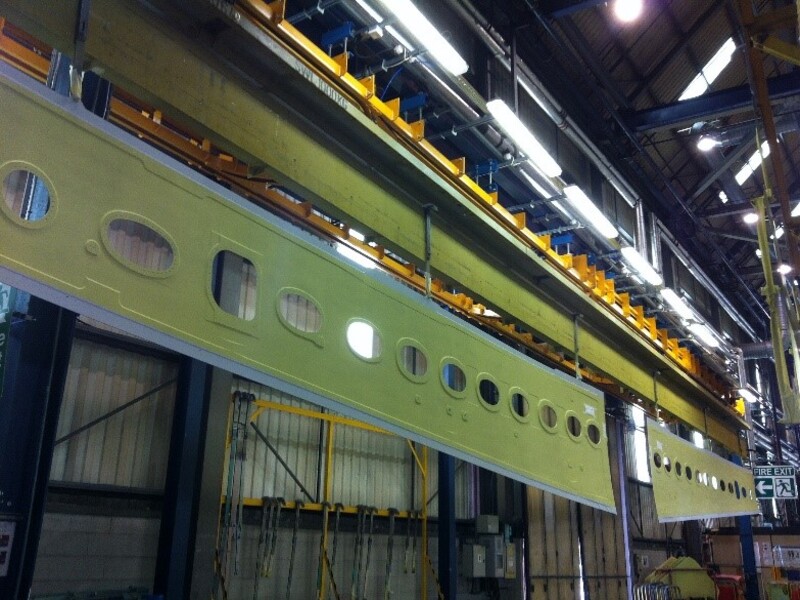
Aerospace
The UK has always had a strong Aerospace presence. BAE Systems Ltd. Located at various sites, manufactures many aerospace and defense vehicles and products. At the Salmesbury Aerodrome site Midland Handling provided a Transporter System that lifts cages of titanium parts for the Eurofighter through special acid treatment tanks.
In Broughton Flintshire Airbus has a factory manufacturing wings for its range of airliners. Midland handling provided an extensive power & free overhead conveyor system to take the wings through a paint plant.
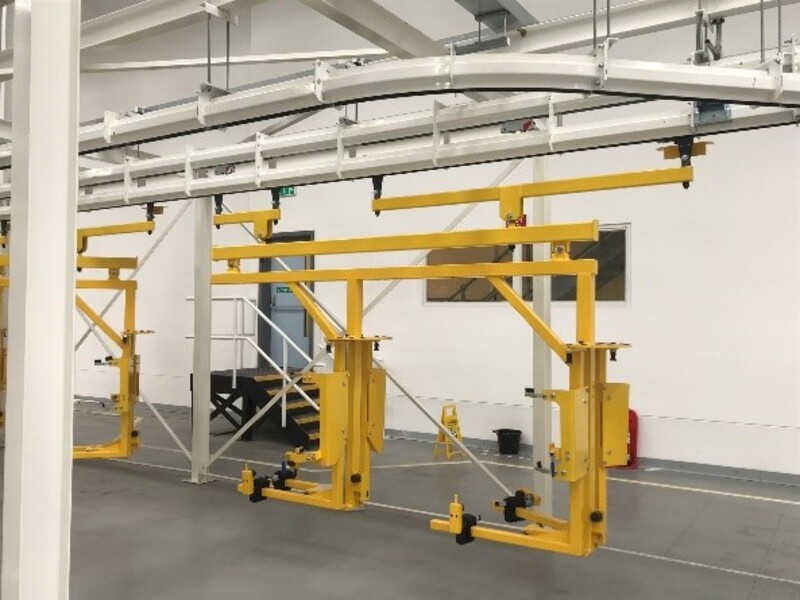
Automotive
With the automotive sector our minds usually go straight to the big car manufacturers but aside from the finished article there are thousands of small to large businesses that service and supply parts that make up these vehicles.
Some of the larger automotive manufacturers in the UK include Nissan, Jaguar Land Rover, Toyota & BMW Mini. Midland Handling supplied an overhead chain conveyor to transport crank shafts at Toyotas engine plant in Deeside. Aston Martin in Wales have two MHE systems for assembly lines as well as JLR is Solihull.
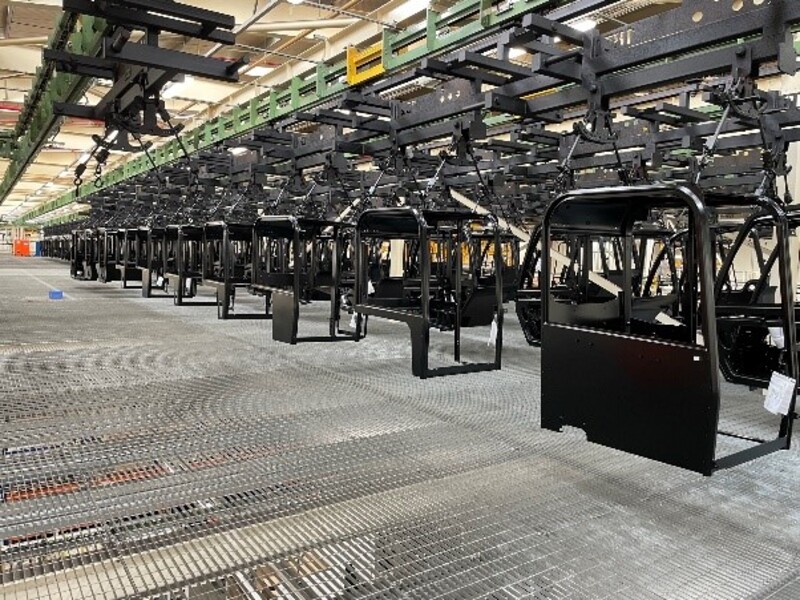
Construction Equipment
JCB Excavators have become one of the leading manufacturers of construction machinery worldwide. Headquartered in Rocester, Staffs the JCB gold and black logo has become a familiar image to many.
Midland Handling have secured a very strong relationship with JCB supplying a total of 7 very large systems over the last 30 years. The most recent being the new cab manufacturing unit JCB Cab Systems relocated to a new state of the art factory just outside Uttoxeter. The conveyor system comprised of 2800m of 406TC Power & Free conveyor on two levels with 7 off external drop section and 4 off specialist oven lifts.